Acumatica Inventory Management Software
Acumatica provides cloud based Inventory Management software that provides real-time access to available inventory, inventory in transit, reorder quantities, and inventory costs so you can efficiently manage your distribution process to improve customer satisfaction while maximizing profits. Acumatica’s cloud inventory management software is a key component of the Distribution Suite and is integrated with the Financial Suite as well as the Order Management and Purchasing Management modules.
Watch Acumatica Inventory Demos:
How to Perform Physical Inventories With Acumatica
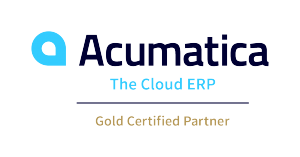
Get started with these helpful resources:
Highlighted Features
Multiple Valuation Methods
Acumatica’s cloud inventory software allows you to value your inventory using standard cost, moving average, FIFO, and item specific methods. You can select a different valuation method for each inventory item. A set of report and inquiry screens provides up-to-date valuations and allows you to make direct adjustments to cost and physical inventory count.
Multiple Warehouses
Acumatica allows you to manage multiple warehouses with location specific inventory quantities, allocations, and costs. For each warehouse you may specify the access rights to determine the group of people who can access warehouse information and enter inventory transactions. In order to trace inventory valuation in the GL, you can assign multiple warehouses to specific inventory accounts.
Lot and Serial Numbering
Acumatica allows you to track inventory by lot or serial number. Lot and serial numbers can be assigned or entered manually when you receive, issue, or assemble inventory items. Serial numbers can be linked with item specific valuation methods to account for the cost of inventory per lot/serial number. Inquiry screens and reports will provide you an option to find out the lot/serial item history.
Additional Features
Inventory Bin/Location Control
Acumatica allows you to create a physical and logical warehouse structure using inventory bins and location controls. For each warehouse location you can specify the types of items and transactions that are allowed, the picking priority, and the cost of the items. Report and inquiry screens allow you to see available inventory and allocation details for each inventory location.
Inventory Subitems
Acumatica allows you to separate items into sub-categories so you can track inventory characteristics such as size, color, and style. You can associate separate cost and quality information with each subitem. Inventory management software reports and inquiry screens allow you to see detailed segment information as well as aggregated inventory totals.
Expiration Dates
Acumatica allows you to assign an expiration date for each lot and serial number so expired items can be deducted from your list of available inventory. Acumatica can automatically issue items with the earliest expiration date to minimize losses. Reports and inquiry screens allow you to monitor expiring items.
Negative Inventory
Acumatica allows a negative inventory balance for an individual item or group of items. Over-issued items will use most recent historical cost until the item is received. When received, the inventory management software will match the receipt cost with issue cost and generate a cost adjustment for the difference. Negative quantities and values may apply to one site or location while aggregated inventory is positive. Appropriate warnings are issued on transactions that will result in negative inventory.
Multiple Inventory Accounts
Acumatica allows you to create multiple inventory accounts and subaccounts for different groups of items so you can maintain a detailed balance of your inventory on the GL. Inventory account and subaccount codes can be derived from the warehouse or the inventory item. When you change an inventory account, newly received inventory will be assigned to the new account while issued inventory will be deducted from the old account until the inventory is depleted.
Transaction Reason Codes
Acumatica allows you to assign reason codes to inventory transactions so you can measure trends and spot problems. Reason codes can be linked to both GL accounts and inventory levels for financial and operational reporting. Subaccounts can be assigned automatically depending upon the type of operation, the warehouse, or the person who enters the transaction.
Two Step Transfers
Acumatica completes inventory transfers in two steps so you can track goods in transit between locations. The first step deducts inventory from the warehouse of origin and increases the Goods in Transit GL account. When goods are received the Goods in Transit GL account is reduced and the destination site quantity and value is increased.
Inventory Allocation
Acumatica maintains detailed cost allocation information on all inventory related transactions. Allocation information is constantly updated for all transactions as well as anticipated receipts and issues. You can drill down the allocation details and navigate to the original documents that results the allocation.
Physical Inventory
Using the physical inventory count features you can organize your goods based on ABC codes and movement classes and conduct regular cyclic count of your inventory. Items that are included in the count are locked in inventory and no operations that affect warehouse quantity are allowed. Once the count is completed you can continue the operation and enter the count result later. Once the count results are entered system will generate appropriate inventory adjustment based on historical snapshot.
Drill Down to Original Document
Acumatica’s inventory management software provides a complete set of inquiry screens and auditing reports that helps you analyze your stock and reconcile your inventory balances. Most reports and inquiry screens allow you to drill down to the original transactions.
Inventory and Warehouse Security
Acumatica allows you to control which users and roles can view and create transactions for inventory items and inventory warehouses in order to improve the accuracy of the data entry and enforce inventory control.
Audit Trail
The Inventory Management software provides a complete audit trail of all inventory transactions. After a transaction is released it cannot be deleted – to correct mistakes, you must enter a correcting transaction to reverse the incorrect entry. The system keeps the details of all Inventory transactions, including the user who entered the transaction and the user who modified the record. The auditing process is simplified by having notes as well as supporting electronic documents attached directly to the transactions.
“We decided to move to Acumatica ERP in Jan 2015. Our partner is Cloud 9 ERP Solutions and we have been very happy with them. They have walked us through the implementation process, dug in and found solutions when we needed to do something a little differently and gone to bat for us when we needed help. Overall, we couldn’t be happier with our move to Acumatica and working with Cloud 9 ERP Solutions.”
Choosing the right ERP Software can be a daunting task. Cloud 9 ERP Solutions can help.