All-in-One Janitorial Software for the Jan San Industry
The Jan San industry faces many challenges, from inventory management complexities to unpredictable demand fluctuations. Acumatica ERP offers a comprehensive janitorial management software solution. Whether you are a Chemical Manufacturer, Distributor or Buying Group, Acumatica has you covered. With real-time visibility into inventory levels and demand forecasts, businesses can optimize their supply chain and avoid stockouts or overstock situations. The integrated manufacturing capabilities streamline production processes, reducing lead times and enhancing efficiency. The advanced analytics provided by Acumatica enable data-driven decision-making, empowering companies to adapt quickly to market changes. Jan San businesses can leverage these technologies to thrive in today’s competitive landscape and overcome challenges.
Cleaning and Maintenance Supplies Distributor Solutions
Cleaning and Maintenance Supplies Distributors encounter numerous challenges in their operations, stemming from the intricate nature of their product sales channels and the numerous prices and costs these channels represent. These challenges are exasperated by shrinking margins and market share as more and more small businesses turn to big box stores or online retailers for their cleaning supplies. These challenges necessitate robust solutions to ensure profitability. Click the + to learn more in each dropdown section.
Supplier Contract Management
These contracts are generally entered between the manufacturer and the ultimate end customer, and distributors are required to maintain and understand the relationships between these two parties. These contracts, in addition to being detailed and difficult to manage as they are generally based on per SKU negotiated pricing, require POD (point-of-delivery) rebate reporting. If products are missed or reporting is not created in the formats acceptable to the manufacturer, the distributor risks selling products at prices that are lower than standard costs. Additionally, for those distributors that pay sales commissions based on a percentage of gross margin, a recalculation of gross margin to reflect adjusted gross for these contracts must be calculated prior to receiving these rebates to compensate salespeople properly.
Acumatica provides the tools to create relationships between suppliers and ultimate customers on a per SKU basis, making rebate reporting efficient and accurate. Acumatica customizations allow the appropriate gross margin to be reported at the time of Order Creation, removing the guesswork in commission calculation.
Gross Profit Adjustments
Acumatica allows you to adjust gross profit converting it from “raw gross profit” (Sales-Cost of Product Purchased) into a fully loaded commissionable gross profit. This fully loaded gross profit can be adjusted with landed costs for transportation and tariffs, or it can be adjusted add other overhead costs like warehousing. Inversely, gross margin adjustments can be made to reduce warehousing and overhead costs and increase margin for certain items, i.e. drop shipped items.
Buying Groups
Buying groups in the janitorial, sanitation, and cleaning (Jan-San) industry are cooperative organizations formed by independent distributors, manufacturers, or suppliers to leverage their collective purchasing power. Acumatica allows for seamless communications making a membership in a buying group efficient and easy. If you are a buying group yourself, Acumatica can support your purchasing and membership initiatives.
EDI
EDI is still a fact of life for most distributors. There are still suppliers and customers who require transactions be sent over a VAN and translated into and from many standard documents. Acumatica and the Acumatica Marketplace provide an abundance of EDI integrations and VANs to fulfill these needs. Acumatica import and export scenarios can be used for those suppliers and customers who would like to automate the passing of documents but would like to use faster and less expensive sFTP protocols for these transactions.
Inventory Planning and Forecasting
Purchase too little and you stifle sales, purchase too much and you lose money on financing costs and dead stock. Achieving that ultimate balance has been elusive to companies who have not deployed a demand planning solution. For Acumatica users, the ultimate balance is achieved with a concrete inventory planning and forecasting tool. Increase inventory visibility, provide accurate forecasts and demand planning, automatically classify every SKU in your portfolio according to sales and velocity to allow you to work on critical items to meet demand. Additionally, predictive ordering enables faster replenishment and a full supplier performance suite to allow you to reduce lead times and improve customer service levels. Acumatica offers many partnered solutions to accommodate your inventory planning and forecasting needs.
Monthly Quotas and Goals
Sales management is crucial to distributors. Setting monthly sales quotas for sales reps in the field and reporting those goals promptly and accurately is a management tool that each distributor requires. Acumatica provides automated reporting of sales goals and actual progress against those goals at pre-decided intervals to improve sales morale and motivation.
Pricing Updates in a Changing Economy
Costs change quickly and without notice in some instances. If your sales prices are static you run the risk of selling items at gross margins less than expected, or even selling at a loss. Using the tools available in Acumatica a distributor can calculate the appropriate selling price of items for every new shipment received. In this way the gross margin can be predictable and selling prices quickly and efficiently updated.
eCommerce and Multi-Channel Marketing
As traditional markets shrink, the ability to sell via eCommerce or through Multi-Channel Markets becomes mission critical. Acumatica is uniquely among ERP Systems being a true cloud offering that is part of the Open API Initiative. This means that a connector to your platform or marketplace probably already exist, which will reduce costs and speed your time to implement, meaning faster to market and faster to sales. Other ERP solutions are forced to use expensive work arounds like iPaaS which add costs and complexity to an ERP integration.
Accurate Financial Results
Acumatica provides not only the operational functionality needed for Cleaning & Maintenance Supplies Distributors, but also delivers best-in-class financial management tools required for ultimate success. Tracking Customer AR, Supplier AP, Inventory Valuation, Cash Management and Financial Reporting in a GAAP Compliant highly secure solution is what you can expect from Acumatica.
Discover How Cloud 9 ERP Solutions Can Transform Your Business
Whether you’re in the Janitorial Sanitation industry as a Supply Distributor, Manufacturer, or Buying Group, Acumatica’s Complete ERP Suite for Jan-San has you covered.
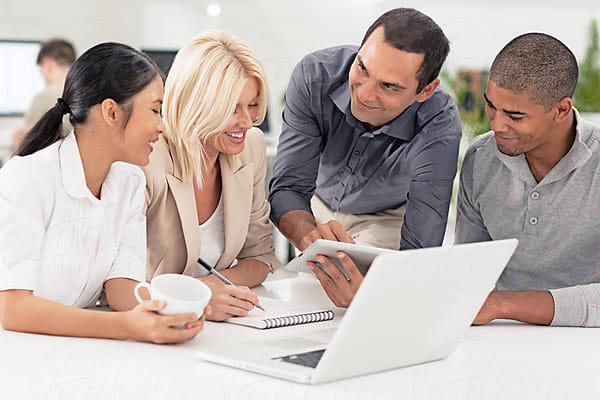
Acumatica for Distributors of Janitorial and Cleaning Supplies
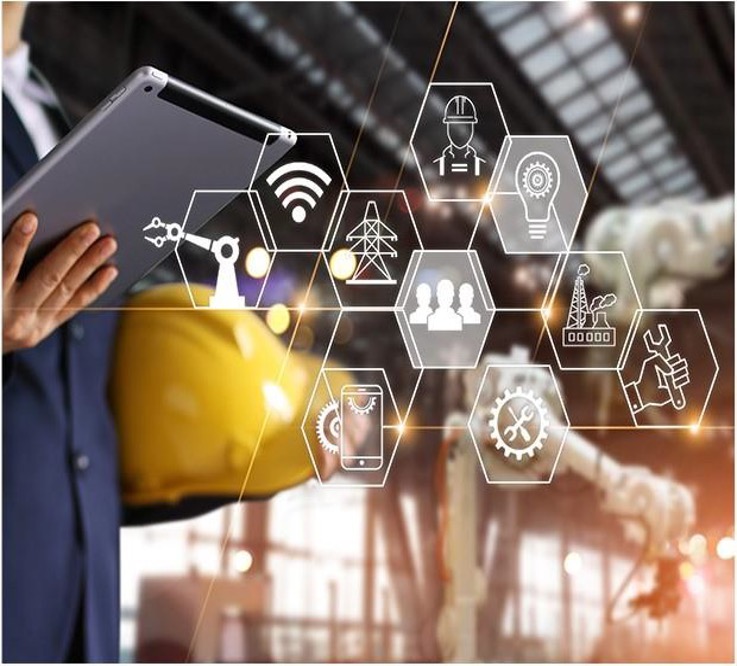
Distributors of janitorial and cleaning supplies grapple with operational inefficiencies like limited visibility and slow deliveries. Acumatica offers a solution by providing real-time insights into operations, enhancing efficiency, and streamlining inventory management. Its scalability ensures seamless growth while maintaining quality standards. With timely insights, businesses can meet customer demands competitively.
The Acumatica Enterprise Distribution Edition consolidates purchasing, warehousing, and sales, streamlining processes into one system. This centralized approach allows for coordinated control of product flow from supplier to customer.
Chemical cleaning solution distributors benefit from Acumatica’s ability to manage inventory mix, product availability, and streamline processes. It recommends purchases based on historical data, manages approval workflows to prevent over-purchasing, and offers flexible fulfillment methods. Moreover, it handles outside communications, EDI, eCommerce, and multi-channel marketing through powerful APIs and third-party solutions, facilitating seamless transactions with suppliers and customers.
Jan San Manufacturers
Acumatica tackles challenges in Jan San Distribution with complete solutions. It offers instant visibility into operations, boosting efficiency. Faster vendor reporting and simplified inventory management ease bottlenecks. Scalability ensures smooth growth in both volume and value while upholding quality and compliance. Timely insights empower decision-making, helping businesses compete by effectively meeting customer demands.
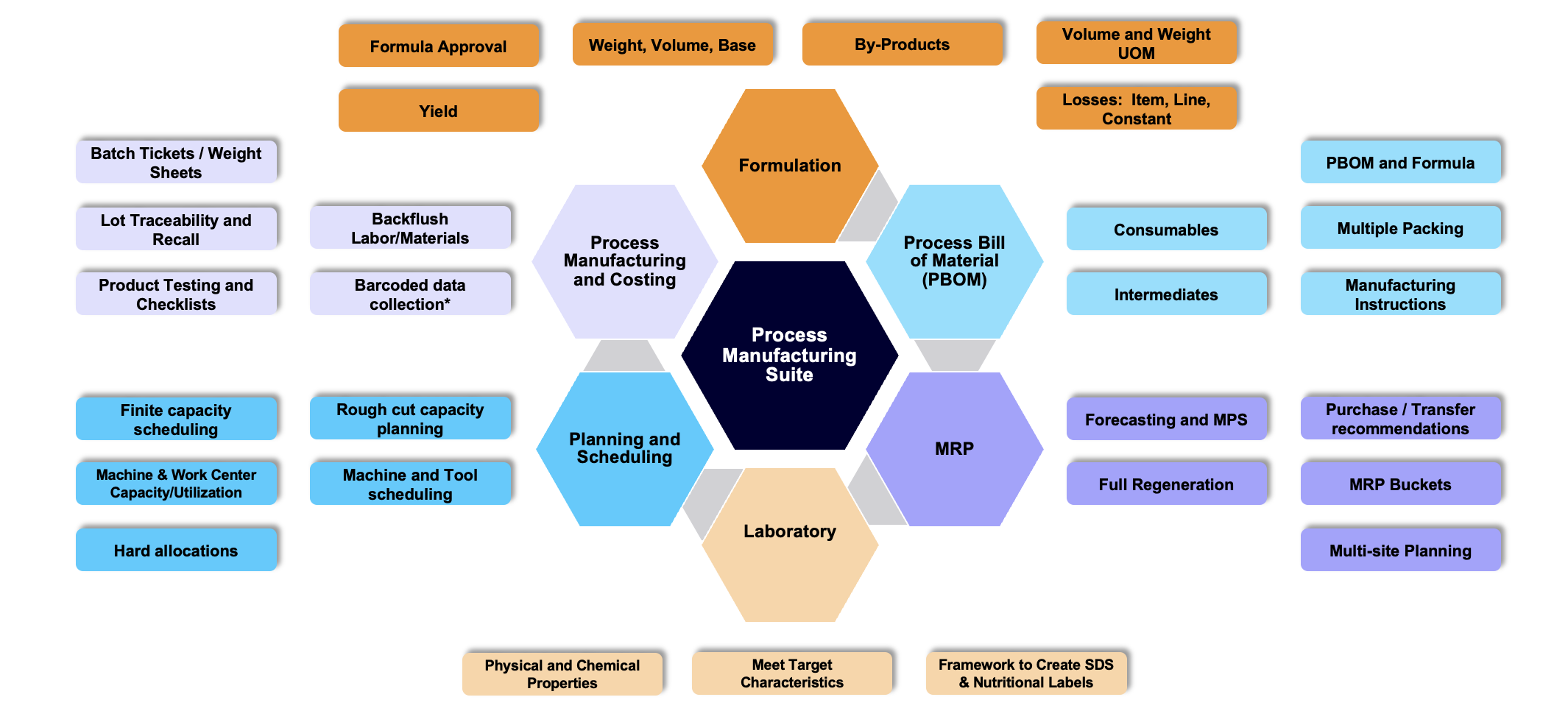
Functional Features for the Jan San Industry
You can explore the innovative solutions and cutting-edge technologies shaping the future of janitorial and sanitation services, and discover how these features can enhance operational effectiveness. Click the + to learn more in each dropdown section.
Formulation and Packaging
Dynamically adjust formulas during both product development and production to meet specified target characteristics.
- Formula version control
- Packaging version control
- Ingredient costs, weights, volumes, counts and multiple UOM’s
- Embedded QC tests and SOP’s
- Product costing
- By-products
- Losses & gains adjustments
- Workflow approvals
- Definition of Labor / Overhead
Process Bills of Material
Extend Acumatica’s Bill of Material for your process manufacturing needs. For example, define multiple packing configurations for the finished product made from the same formula.
Process Order Management
Create and schedule the optimal number of batch jobs required for a product formula and its multiple packaging configurations.
Costing and Comparative Analysis
Roll up existing and theoretical product costs, as well as fixed, tiered, and scalable costs, to formulas, intermediates, and finished goods during product development.
Traceability
Quickly track and trace suspect materials from receiving through shipping, shipping back to receiving, or anywhere within WIP.
Weighing Sheet and Batch Record
Stage and weigh materials that will be used in the production process with efficiency and accuracy.
- Batch job formulation adjustments
- Batch job dependencies and linkages
- Consolidate and optimize batch jobs based upon item and/or order attributes
- Batch job scaling & sizing
- Equipment & labor assignments
- Inventory allocation criteria & order reservations
- Bulk inventory pulls & staging
- Lot number auto generation
- Partial batch job closures
- Automatic inventory backflushing
- Theoretical vs Actual Cost analysis
- Mobile Task execution
Mobile Task Execution
- Warehousing Execution: Receiving, Putaway, Physicals, Cycle Counting, Transfers, Adjustments, Picking, Shipping
- Manufacturing Tasks: Weighing, Issuing
- Quality Tasks: Inspections, Checklists, QC Tests
- Labor
- Role-Based Menus/Task Assignments
Compliance Reporting and Labeling
Keep compliant with industry-specific and federal regulations, lot traceability reports, transactional audit reports, and shipping documentation.
- Lot Traceability & Recall
- Version control
- Certificate of Analysis
By-products
Correctly manage and cost by-products.
Quality Management
Integrate end-to-end quality control with the Quality Management Suite for Acumatica solution.
- QC tests & SOPs embedded within specifications
- Item inspection plans & checklists
- Order type inspection plans & checklists
- Inventory stability tests
- Vendor/Customer inspection plans & checklists
- Deviation management
- Customer complaints & adverse event management
- Non-conformances & CAPA
- Audit history
- COA generation
- AQL & RQL
- Sampling plan
- Mobile Task execution
Reporting and Analytics
Create, manage, and distribute reports that improve transparency and decision-making.
Laboratory
Define and track an unlimited number of physical and chemical properties. Modify or develop a new formula/recipe based on these properties and dynamically adjust
them to meet target characteristics.
Product Development / R&D (roadmap)
Engage in product testing and development without interfering with current production and document testing notes to ensure consistency and quality.
Inventory Management
- Multiple SKU UOM tracking & conversions
- Item Master industry specific attributes
- Expiration date tracking
Key Benefits
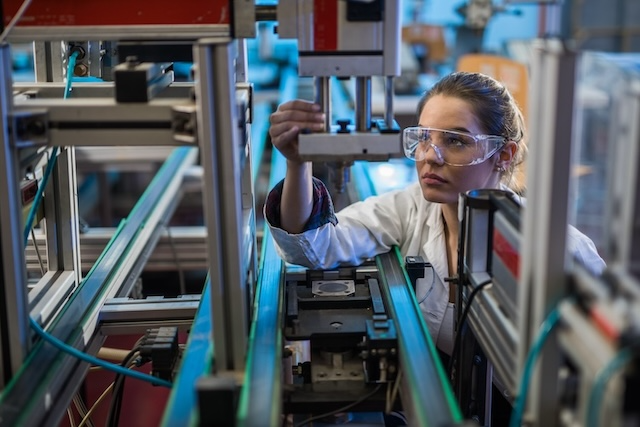
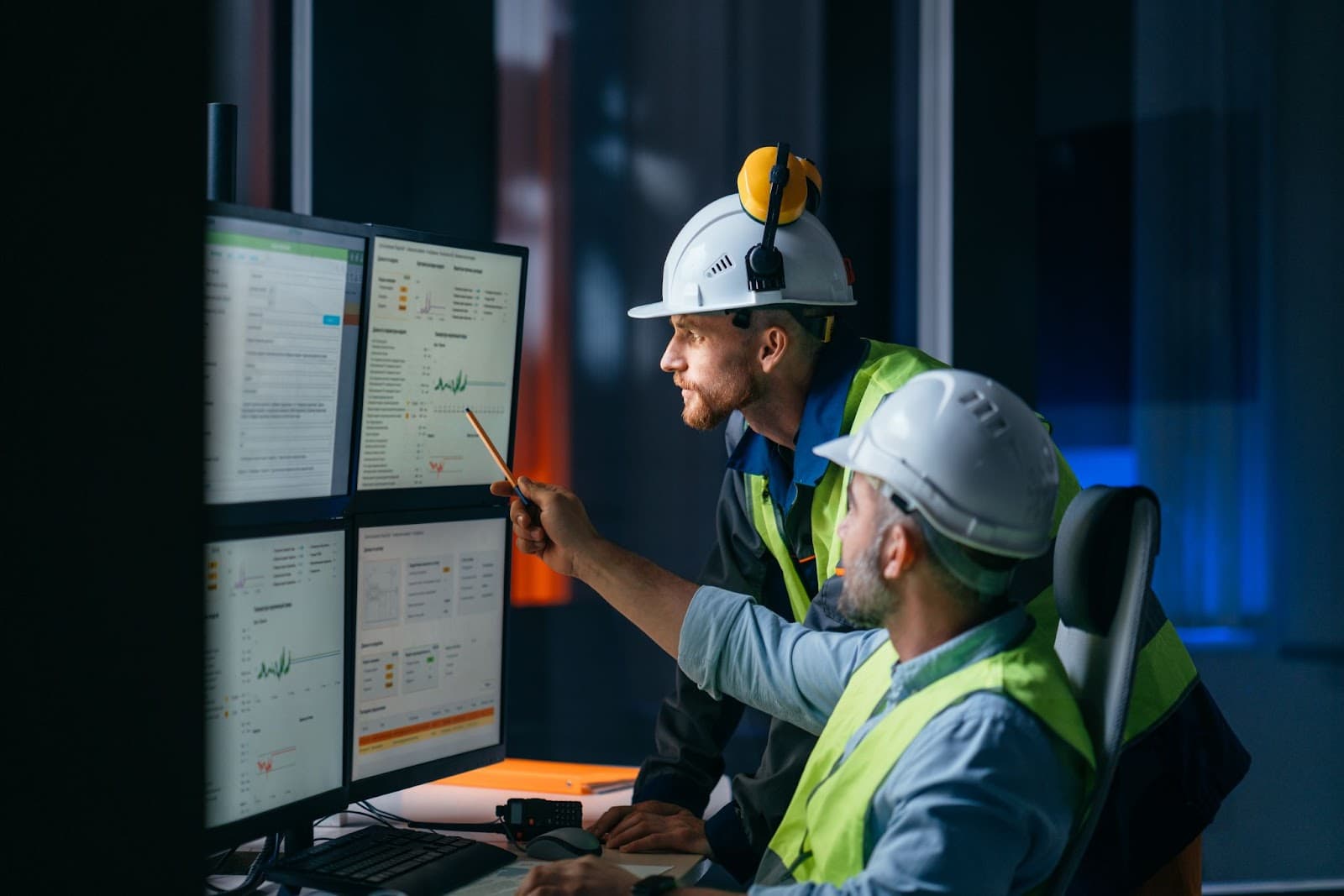
Application Benefits
- Extends Acumatica to deliver an industry-specific ERP solution for process manufacturers
- Fully integrated with Acumatica Manufacturing Edition – MRP, Planning and Scheduling, etc.
- 100% developed using the Acumatica framework and database
Business Benefits
- Increase visibility and control
- Streamline operations
- Accelerate product development
- Balance inventory levels
- Scale up production
- Ensure quality and compliance
- Respond to changing customer demands
- Make better decisions faster
- Strengthen your competitive advantage
Key Capabilities
Gain more control over batch production of finished goods, including the by-products
Manage QC activities and generate industry-specific compliance labeling and reports
Create separate formulas and packaging specifications
Dynamically adjust ingredients to meet target values of intermediates and finished goods
Analyze costs and yields
Safeguard formulas or recipes
Support for manufacturing instructions and consumables
Define and track losses at various levels
Issue inventory to production based on those passed through QC
Customer Testimonial
Since 1972, Trace Mineral’s branded products have been recognized around the world as a pioneer of ionic trace mineral products that have supported consumers in living healthy lives.
“Trace’s implementation of eWorkplace Apps integrated process and quality management
solution into its current Acumatica accounting and distribution systems will provide Trace
with a complete ERP system that will allow it to continue to meet and surpass its goals in
manufacturing and quality. This will be accomplished by using a quality system to
quarantine and test items throughout the receiving, production and shipping process and
ensure tight control of production via a formula module that supports both powder and
liquid formulas and bill or materials that supports multiple pack sizes.”
— Kelly Jones, Director of Quality and Purchasing, Trace Minerals
Built by Acumatica, Delivered by a Top Partner
Though many companies claim to work with manufacturing firms, it’s all about finding the one who can deliver for your specific business needs. Few solutions exist today that can handle both the financial, process, and inventory management needs of companies like yours, and even fewer partners know how to deliver such a solution.
At Cloud 9 ERP Solutions, a Gold Certified Acumatica Partner, we have worked with companies like yours to configure and deliver Acumatica Cloud ERP, a product ready and able to handle your challenges.
Get to know more about how we work, who we’ve helped, and why we’ve been a leader in the business for nearly three decades by contacting us for a free consultation.
Choosing the Right ERP Software Can Be a Daunting Task. Cloud 9 ERP Solutions Can Help.
You have questions, we have answers. Schedule a no-obligation conversation.
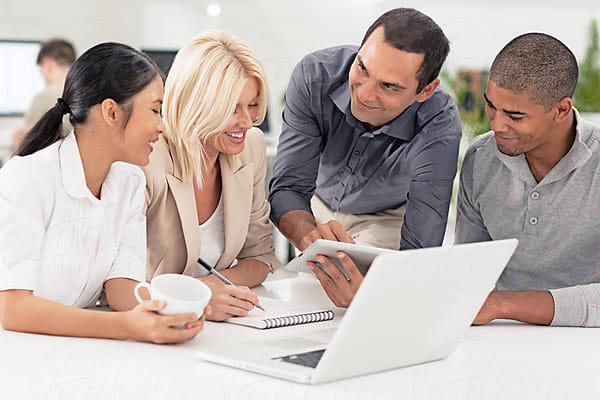